Understanding What is Porosity in Welding: Reasons and Solutions
The Scientific Research Behind Porosity: A Comprehensive Guide for Welders and Fabricators
Understanding the intricate devices behind porosity in welding is vital for welders and fabricators making every effort for flawless craftsmanship. From the structure of the base products to the complexities of the welding process itself, a plethora of variables conspire to either worsen or reduce the visibility of porosity.
Comprehending Porosity in Welding
FIRST SENTENCE:
Exam of porosity in welding reveals vital insights into the honesty and quality of the weld joint. Porosity, characterized by the visibility of cavities or gaps within the weld metal, is a typical problem in welding processes. These spaces, if not effectively dealt with, can jeopardize the architectural integrity and mechanical residential or commercial properties of the weld, leading to potential failings in the ended up item.

To discover and evaluate porosity, non-destructive testing approaches such as ultrasonic testing or X-ray evaluation are commonly used. These strategies enable the identification of internal problems without jeopardizing the stability of the weld. By examining the size, form, and circulation of porosity within a weld, welders can make enlightened choices to boost their welding procedures and attain sounder weld joints.
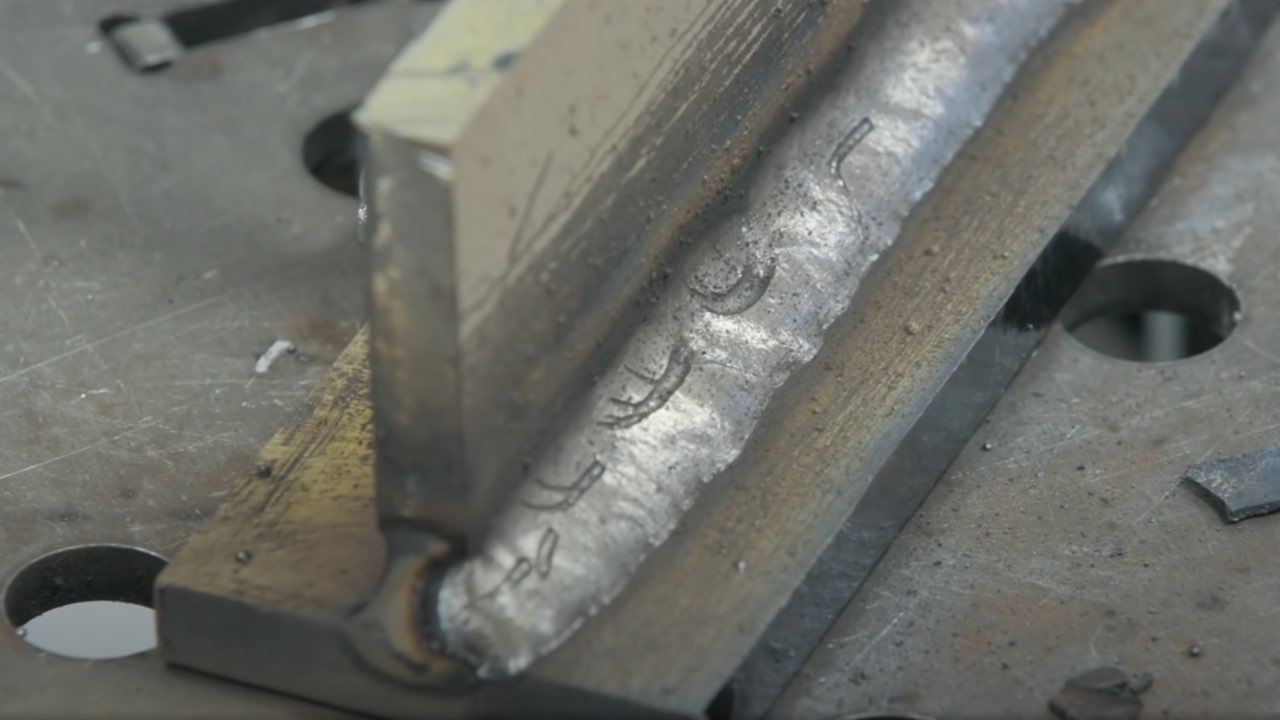
Elements Influencing Porosity Formation
The event of porosity in welding is influenced by a myriad of variables, ranging from gas securing efficiency to the intricacies of welding specification setups. Welding parameters, consisting of voltage, present, take a trip speed, and electrode kind, also effect porosity development. The welding technique used, such as gas metal arc welding (GMAW) or secured metal arc welding (SMAW), can influence porosity development due to variations in warmth circulation and gas coverage - What is Porosity.
Impacts of Porosity on Weld Top Quality
The existence of porosity additionally compromises the weld's resistance to corrosion, as the trapped air or gases within the gaps can react with the surrounding environment, leading to destruction over time. In addition, porosity can impede the weld's capability to stand up to pressure or impact, more endangering the general quality and integrity of the welded framework. In important applications such as aerospace, vehicle, or structural constructions, where safety and security and longevity are vital, the harmful effects of porosity on weld high quality can have serious repercussions, stressing the significance of minimizing porosity via appropriate welding techniques and treatments.
Techniques to Decrease Porosity
Additionally, making use of the proper welding criteria, such as the correct voltage, present, and take a trip rate, is crucial in avoiding porosity. Keeping a regular arc size and angle during welding also assists minimize the probability of porosity.

Using the appropriate welding strategy, such as back-stepping or utilizing a weaving movement, you could try these out can additionally assist distribute heat equally and lower the possibilities of porosity formation. By applying these methods, welders can efficiently decrease porosity and create top quality bonded joints.
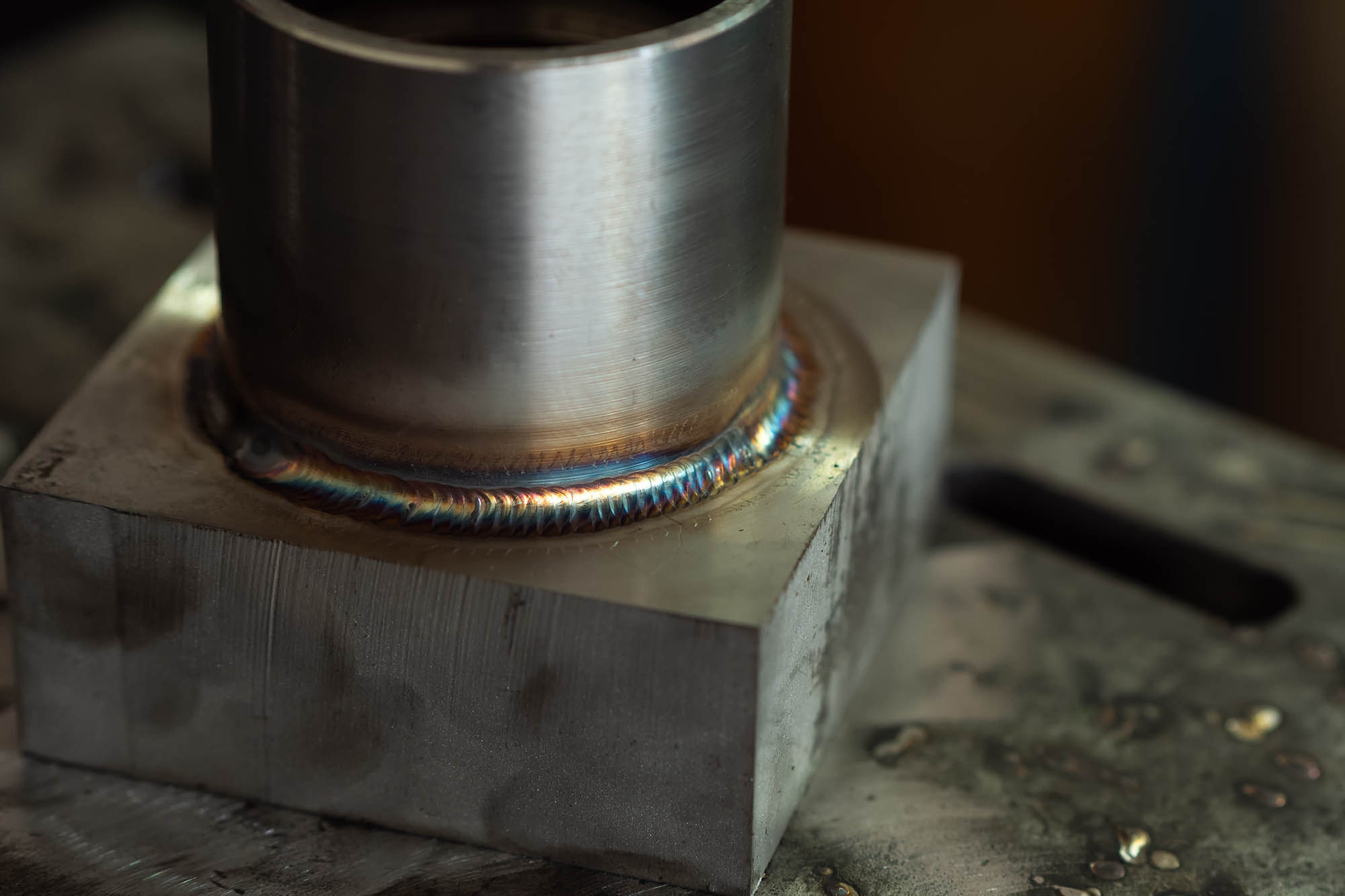
Advanced Solutions for Porosity Control
Executing cutting-edge innovations and cutting-edge methods plays an essential role in accomplishing premium control over porosity in welding procedures. Furthermore, utilizing advanced welding techniques such as pulsed MIG welding or customized ambience welding visit this page can also assist alleviate porosity problems.
An additional advanced service entails making use of advanced welding devices. For instance, making use of equipment with built-in functions like waveform control and advanced power sources can improve weld top quality and official source minimize porosity threats. The execution of automated welding systems with accurate control over specifications can significantly lessen porosity flaws.
In addition, including sophisticated monitoring and inspection innovations such as real-time X-ray imaging or automated ultrasonic screening can assist in discovering porosity early in the welding procedure, permitting for instant restorative activities. In general, incorporating these advanced services can substantially improve porosity control and enhance the total quality of welded elements.
Final Thought
In verdict, understanding the science behind porosity in welding is important for welders and fabricators to produce high-quality welds - What is Porosity. Advanced remedies for porosity control can additionally enhance the welding process and make certain a solid and trusted weld.